Stormseal is a polyethylene film that heat-shrinks to securely wrap a damaged roof or structure.
Unlike tarpaulins, Stormseal stays put until permanent repairs can be made, resisting wind, rain and hail and preventing further distress and costly damage.
This award-winning, Australian innovation has now protected more than 9,000 buildings globally and helps businesses and communities recover faster after disastrous weather.

The Stormseal Story
Read about how the idea for Stormseal was created and the team behind this innovation.
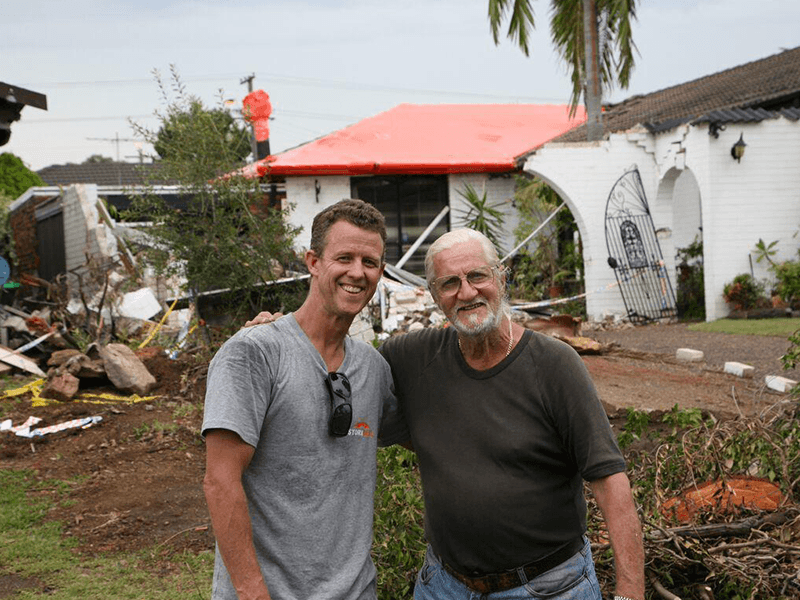
Testimonials & Case Studies
Putting a smile on the face of a previously traumatised victim of extreme weather is a huge reward for Stormseal installers.
Awards
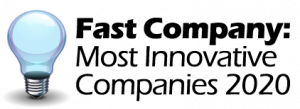
Ranked #5 in Fast Company’s Most Innovative Companies 2020 in the Asia-Pacific
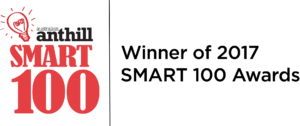
Winner of Anthill’s SMART 100 2017
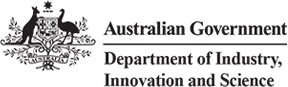
Endorsed by the Australian Federal Government via the Accelerating Commercialisation program
Stormseal is proud to be a member of
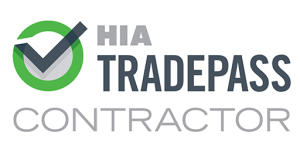
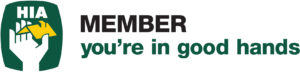
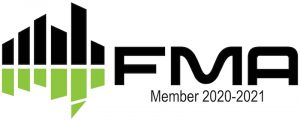
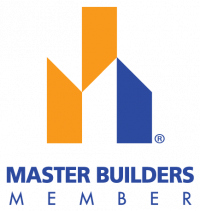
Australian Capital Territory
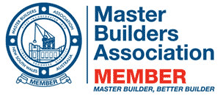

Get Stormseal
To find out more about Stormseal, give us a call on 02 9599 3335, email info@stormseal.com or send a message on our contact page.
You can also find your closest installer using our interactive map.